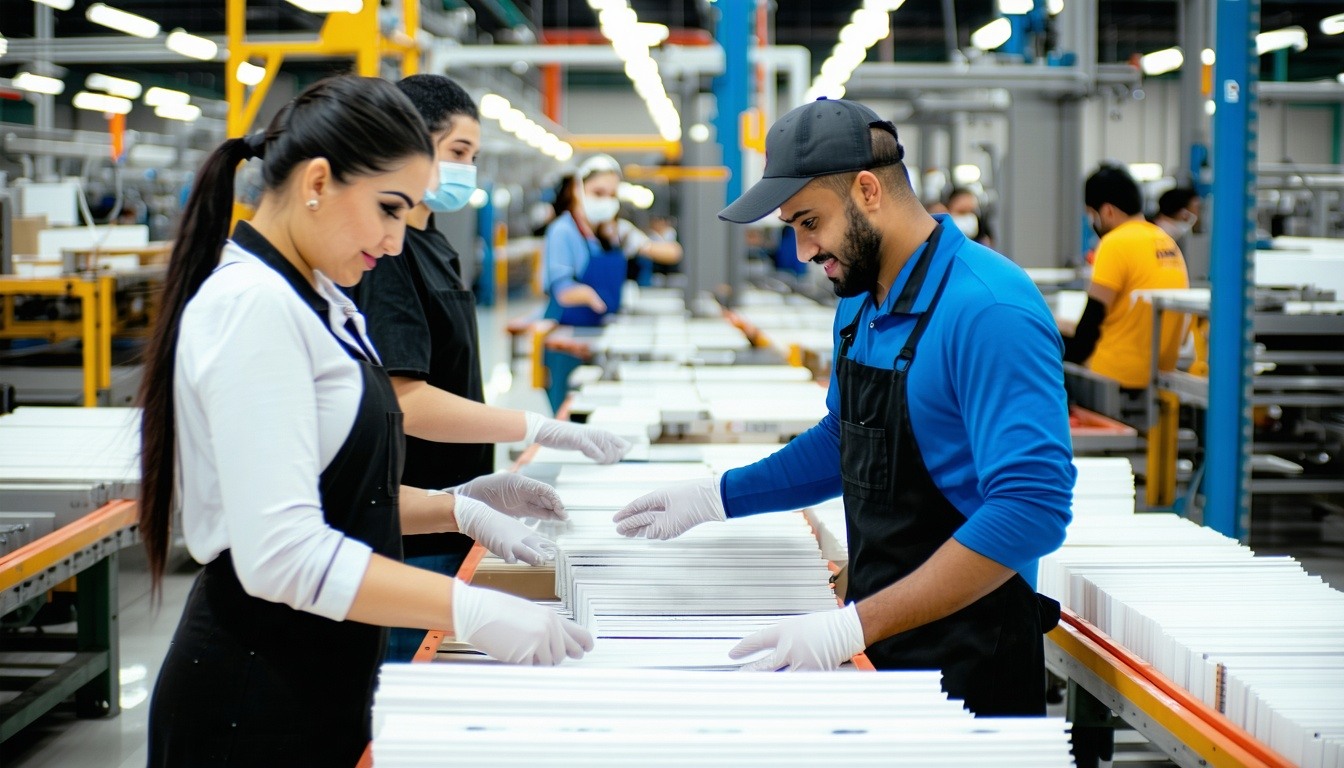
Your Freight's On the Move — But Is Linehaul Operations Keeping Up?

In Linehaul, freight usually isn’t the problem.
It’s everything around it.
A driver calls mid-route with missing details.
A load stalls because no one followed up.
A shift change happens — and no one knows what got done, what’s pending, or what was missed.
Your team is doing what it takes to keep things moving. But when tracking, handoffs, or communication break down behind the scenes, it shows up fast: in late deliveries, double work, and dispatcher burnout.
🔍 The Real Bottlenecks Behind the Wheel
It’s not the trailers. It’s not the trucks.
It’s the missing structure in your day-to-day ops.
You’ve probably seen it happen:
-
Load details scattered across inboxes, Slack messages, and spreadsheets
-
Drivers calling mid-route for contact info or missing instructions
-
Shift handoffs done verbally or not at all — leading to gaps or duplicate work
-
Delays, breakdowns, or issues tracked inconsistently (or not at all)
-
Updates and exceptions shared, but never followed up or closed out
In high-velocity environments like linehaul, these gaps don’t just slow you down — they compound.
🧠 Why Most Fixes Don’t Stick
It’s not that your team isn’t trying.
It’s that most “fixes” require new habits, new tools, or new people — and no one has the bandwidth to implement them properly.
What usually happens:
-
Someone builds a Google Sheet… that gets updated for a week, then forgotten
-
A new platform gets rolled out… but no one uses it because it’s overkill
-
Teams fall back into old habits because the process relies on memory, speed, or someone “checking in” when there’s time
That’s why linehaul ops breakdowns rarely happen all at once — they happen slowly, every time something isn’t logged, handed off, or closed out.
🛠️ Where to Start Tightening Things Up
Whether you’re running on spreadsheets or a full TMS, operational breakdowns usually happen between systems — not inside them. These are a few simple ways to bring structure back into your process without disrupting the whole stack:
✅ Build a Load Visibility Tracker
Your team can’t act on what they can’t see. If dispatch, ops, and leadership are all referencing different systems (or none at all), things fall through. A simple shared board or load tracker — even in Airtable or Trello — can give everyone a unified view of what’s in motion, what’s delayed, and what still needs attention. This helps teams prioritize in real time, reduces confusion across shifts, and makes load management more proactive instead of reactive.
✅ Standardize Driver Instructions
Drivers should never have to call mid-route to ask, “Who do I talk to when I get there?” A consistent instruction format — whether printed, texted, or shared digitally — should include load number, pickup and dropoff details, access notes, contacts, and any client-specific instructions. The more consistent this is, the fewer questions dispatch has to answer during the day. And that means fewer delays, less friction, and a smoother experience for both drivers and customers.
✅ Use a Shift Change Checklist
A lot can go wrong when one dispatcher logs off and another logs in — especially if handoffs rely on memory or hallway conversations. A shift-change checklist ensures the next team knows what’s still pending, what’s in motion, and what escalations need attention. When you bake this into your process, you reduce duplicate work, missed follow-ups, and the classic “I thought someone else was handling it” moment. Over time, it leads to smoother transitions and stronger team accountability.
✅ Set Up Simple Exception Logging
OS&D issues, missed appointments, equipment delays, breakdowns — most teams handle these in the moment, but don’t track them consistently. A lightweight exception log (form, dashboard, or shared doc) gives your team a place to record what went wrong, who’s handling it, and what follow-up is needed. Not only does this help ensure nothing gets dropped, but over time it becomes a valuable dataset for identifying patterns and solving recurring problems upstream.
✅ Streamline Load Intake
New loads often come in from brokers, customers, or partners — and each one brings its own format, urgency, and gaps. Instead of scrambling to make sense of every request, create a clean, standardized intake form. Include the essentials: pickup/delivery, timelines, equipment needs, and any client-specific quirks. This gives dispatch a complete picture from the start, prevents back-and-forth just to assign a load, and ensures your team starts every job on solid footing.
🧰 Task-Based Support That Keeps Freight Moving
Sometimes you don’t need a new system — you just need someone to step in and clean up what’s slipping.
That might look like:
-
Building the exact workflow your team needs to tighten dispatch handoffs
-
Organizing load updates so dispatch, ops, and drivers stay on the same page
-
Handling the exception tracking no one else has time for
-
Turning what’s “in someone’s head” into repeatable processes
It’s not about adding overhead. It’s about restoring flow behind the freight.
✅ Your Freight’s Moving. Let Ops Catch Up.
Your freight’s moving.
Now it’s time to tighten the workflows behind it — before things slip through the cracks.